
How Spitfires keep flying – the story of the propeller
Vintage Spitfires flying today
The Supermarine Spitfire was designed in the 1930s, using the very latest in metallurgy and manufacturing technology. While it was all highly advanced for its time, as a tool of war, the Spitfire was only intended to last for perhaps a few hundred hours before being lost in combat, damaged in accidents or simply scrapped.
With all remaining Spitfires now around 80 years old and some having flown for thousands of hours, even the most ‘original’ airframes are now likely to comprise many exchanged or replacement parts.
Spitfires and spare parts – the biggest challenge
If you’re lucky enough to be the owner of one of these 60 or so airworthy Spitfires left in the world, then finding spare parts to keep it flying will be one of the biggest ownership challenges to face.
Indeed, the rapid rise in demand during the past decade for passenger flights in two-seater Spitfires has helped drive demand for spare parts even further, as the number of aircraft in regular use increases.
Like any mechanical object, Spitfires are designed to ‘consume’ a wide variety of parts, which require regular replacement according to age and use. With the growing interest in collecting, restoring and flying classic ‘warbirds’ over the last 30 years, most remaining original parts have now long since been used.
Any parts that were on the market have been squirrelled away by enthusiasts and collectors keen to own a tangible piece of the Spitfire legend. So what help is available in your Spitfire parts quest?
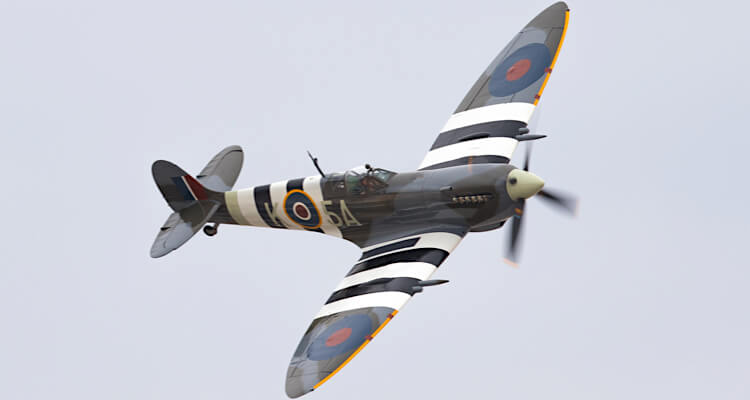
The answer is with WW2 aviation specialists
Fortunately, here in the UK and around the world, a number of specialist firms have developed expertise in re-manufacturing spare parts for Spitfires and other classic aircraft to meet this need.
The metal parts which make up the actual airframe are relatively simple to reproduce, assuming the correct type and quality of metal is available in order to meet the original design specifications.
If not, special batches of raw material have to be commissioned – all of which comes at a high cost (of course!). A second barrier to overcome is how to replicate original manufacturing techniques in a way that is viable for low volume.
A good example of success here is for the manufacture of wing spars, which are hand-crafted from unique concentric squared tubes. These spars help give the Spitfire its distinctive wing shape and are needed for new restorations and to keep existing aircraft in the air.
The quest for the perfect Spitfire propeller
Another essential, but surprisingly difficult part to reproduce is propellers. These are what transmit the power of the Spitfire’s famous Rolls Royce Merlin engine at speeds of up to 400 mph.
Both the complex metal central hubs that attach to the engine and the compressed wooden blades that make up the Spitfire propeller have long been in short supply.
For decades, replacement propeller blades were only available from a large manufacturer based in Germany – a deep irony for Spitfire owners and enthusiasts alike.
Worse still, was the fact that the modern blades were made to a different standard, which slightly restricted the pilot’s ability to fly the aircraft to its full potential.
For several years, Spitfire owners had been asking Hercules, the specialist Cotswolds-based manufacturer of wooden propellers, if it was possible to make Spitfire blades to the original specification.
A chance discovery
At the time, the original information and data detailing the complex shape and dimensions to make the propeller blades was simply not known.
Then, one day, Hercules founder Rupert Wasey received a phone call from a local aviation company that was throwing away some old plans for different propeller types.
He went over to look through the pages and suddenly found what had been lost for decades – an original drawing of a Spitfire propeller!
This precious and elusive drawing was produced in 1942, at the height of World War Two, probably by one of the team of women working in the drawing office while the men were away fighting.
The discovery of this document finally opened the door to remanufacturing to the original wartime specification using the correct materials.
Getting approval for the modern-day Spitfire propellers
Despite Hercules using modern manufacturing techniques perfected over many years, it has been a long and slow process to get approval for the newly-produced blades.
Everything has to be made from the correct combination of wooden materials and then tested physically. Sample blades were produced and pulled with hydraulics until they broke, to measure the forces and ensure that they would stand up to hard use.
Then late in 2020 in the midst of the pandemic, all the research and hard work paid off, as the Hercules Spitfire propeller blades were finally approved for flight by the UK Civil Aviation Authority.
Tested (and approved) by Biggin Hill Heritage Hangar pilots!
The first propeller was air-tested on one of several Spitfires based at the Biggin Hill Heritage Hangar in Kent and immediately the pilot reported that it was a revelation.
The original design, now reproduced to the highest quality and tolerances, gave reduced vibration, improved smoothness and for the first time since the war, allowed full use of the Spitfire’s legendary power and performance. A veritable success story for Hercules.
The living legacy of the Spitfire
All Spitfires represent a key piece of Britain’s and the world’s history. The opportunity to fly in a Spitfire as a passenger is thanks in part to the current generation of specialist suppliers and manufacturers like Hercules, who work hard to produce the parts needed to keep these magnificent planes in the air. Their efforts help keep the memories of the achievements of the wartime pilots alive, at the same time allowing you the chance to make memories of your own with a flight of a lifetime.
If this is your dream, Into The Blue has a wide range of Spitfire flight experiences available at Biggin Hill and other airfields around the UK.